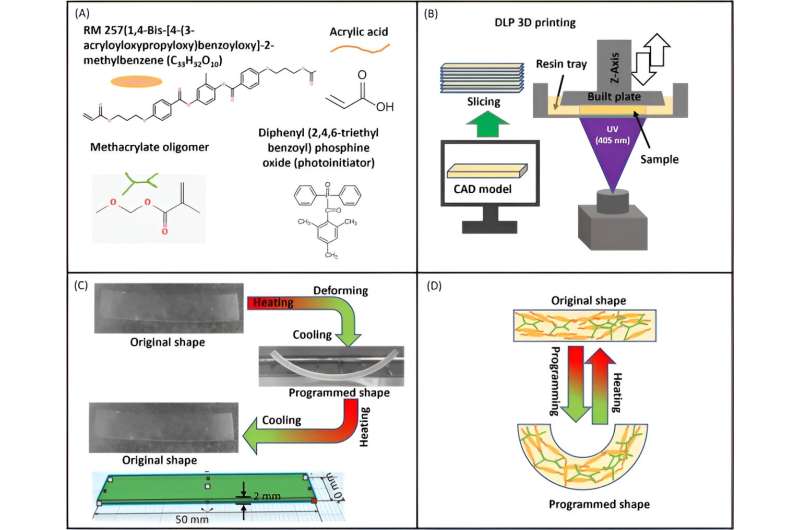
Shape-memory polymers or shape-shifting materials are smart materials that have gained significant attention within materials science and biomedical engineering in recent years to build smart structures and devices. Digital light processing is a vat photopolymerization–based method with significantly faster technology to print a complete layer in a single step to create smart materials.
Fahad Alam and a team of scientists in electrical and computer engineering, and nuclear engineering at the King Abdullah University of Science and Technology, Saudi Arabia developed a facile and fast method to 3D print shape-memory polymer-based smart structures with a digital light printing 3D printer and custom resin.
They combined a liquid crystal (a material that can change its shape with temperature) with resin, to introduce shape-memory properties to directly 3D print thermoresponsive structures—while avoiding the complexity of resin preparation. The team printed the structures with different geometries and measured the shape-memory response. The shape-memory polymers can be conveniently prepared for use as smart tools, toys, and meta-materials.
The paper is published in the journal NPG Asia Materials.
Shape-memory polymers
Shape-memory polymers belong to a class of dual-shape smart polymers that can undergo mechanical deformation and return to their original shape in response to environmental parameters. The shape-memory polymer recovery depends on the application of external stimuli such as heat, light, electricity, humidity, and pH changes.
Such materials are shape-shifting constructs that have gained considerable interest in recent years due to their versatility and industrial viability. The research team demonstrated 4D printing shape-memory polymers via digital light processing; a 3D printing method based on vat photopolymerization. The outcomes highlighted the suitability of 3D-printed complex structures for a variety of applications.
Creating the shape-memory effect
The research team investigated the shape-memory effect of the 3D printed samples by studying the shape inducting and recovering process. The method allowed easy and high-resolution printing of intricate 3D designs. These constructs are useful across a variety of applications as flexible smart patches, size-variable mechanical tools, and deformable toys. In this work, Alam and colleagues developed a shape-memory polymer based on a liquid crystal mixed with a photocurable resin, to develop a semicrystalline polymer and described its mechanism-of-action, based on previous studies.
The team observed the internal morphology of the 3D printed cross sections with or without liquid crystals by using scanning electron microscopy. They then observed the responses of shape-memory polymers relative to their capacity to recover after load-bearing. The present work showed the influence of 3D digital light processing to create shape-memory polymers with 4D effects. The scientists quantified the shape-memory response to show the recovery angle ratio versus time.
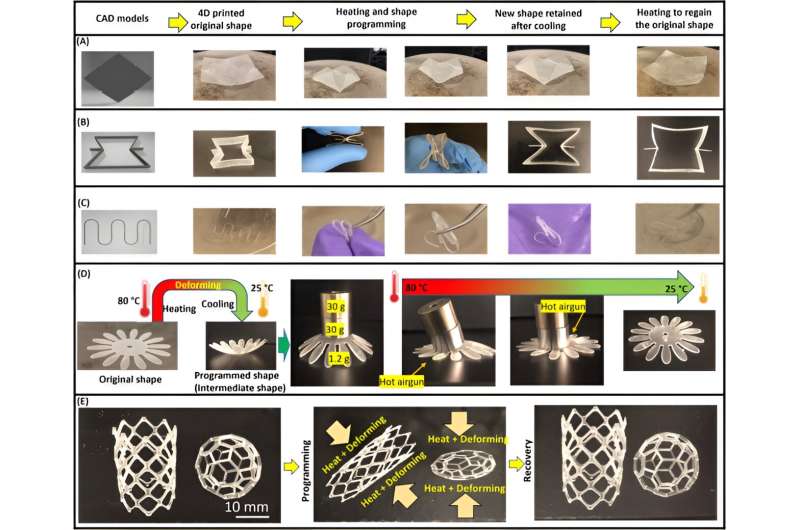
Tunable mechanical properties
The researchers explored the promising applications of 3D-printed smart memory polymers. To accomplish this, Alam and colleagues determined the mechanical properties of the materials by conducting tensile tests on a dog-bone specimen, to show how the mechanical properties of printed materials can be tuned by regulating the shape of the lattice structures.
They confirmed the mechanical tunability of smart materials by conducting finite element simulations, and compared the experimental results with tensile tests from the finite element analysis. The mechanical performances of the 2D lattices observed through experiment and predicted via simulation agreed. Based on the flexibility and stretchability, Alam and team tested the samples for strain testing and for joint moving sensing applications.
To facilitate joint motion via polymer integration, the scientists applied a nano-silver-based conductive coating as an electrode, which required further optimization of the printing parameters. The scientists measured the changes in electrical resistance by stretching and compressing the structure to facilitate movement in patients.
The results of resistance measurement of the prepared lattice electrode patch showed its potential for use as a smart patch for joint-movement sensing; this can be applied to a human knee, elbow joint, artificial limb, or real limbs to sense movement. Such electrode patches can be customized to the size of the patient under easy and fast manufacturing processes.
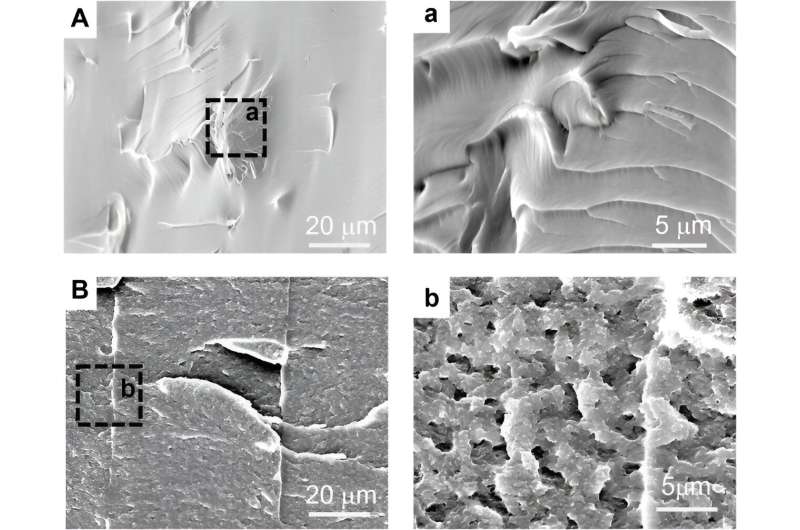
Outlook
In this way, Fahad Alam and team presented a method to 3D print smart materials by first using shape-memory polymers for easy and fast manufacture through digital light processing. The scientists customized the 3D-printed objects to create structures that changed with time, this is known as 4D printing. They achieved this by combining liquid crystals with a resin, and printing it by using a commercial desktop printer. The researchers used the method to manufacture a variety of complex objects including lattice patches, foldable toys, smart packaging, and mechanical wrenches.
The scientists subjected these objects to heat, to temporarily change their shape, and for subsequent shape recovery applications. The team used tensile tests to show the adjustable nature of shape-memory polymers, to meet specific applications in biomedical engineering. Such 3D-printed lattice patches are well suited for strain sensing in joint movement applications. The researchers recorded the changes in electrical resistance from the 3D-printed smart patch to detect the movement in artificial limb joints and arms of patients.
More information:
Fahad Alam et al, Swift 4D printing of thermoresponsive shape-memory polymers using vat photopolymerization, NPG Asia Materials (2023). DOI: 10.1038/s41427-023-00511-x
© 2023 Science X Network
Citation:
Swift 4-D printing with shape-memory polymers (2023, December 22)
retrieved 22 December 2023
from https://phys.org/news/2023-12-swift-d-shape-memory-polymers.html
This document is subject to copyright. Apart from any fair dealing for the purpose of private study or research, no
part may be reproduced without the written permission. The content is provided for information purposes only.